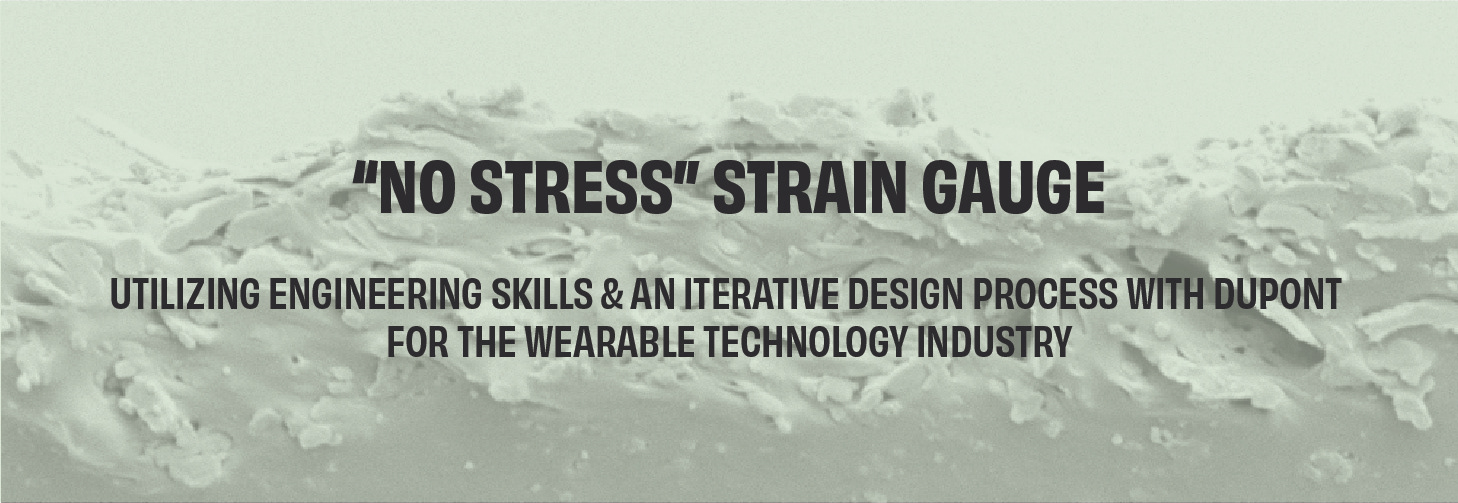
Role
Research, Mechanical Testing, Ideation, Documentation & Editing
Project Collaborators: Josh Dickerson, John Griffiths
Context
DuPont, in leading development of stretchable electronic inks, desired to expand its reach into the wearable technology industry by creating a product that was functional, comfortable, rugged/washable, and able to integrate with their current manufacturing. With this in mind, the DuPont team sponsored a senior design project in the NC State University Department of Materials Science & Engineering to design a solution that aligns with the desired pathway of the group with hopes to make a system that will be compatible with future products in the athletic and medical markets, among others.

deliverables
We successfully met the objectives of the senior design project centered around characterizing material performance and designing a screen-printed strain gauge to report change in resistance. We also concluded that the investigated printing materials were inadequate for DuPont’s intended purposes through mechanical testing and made a next step suggestion to choose a new backing material for their prints.
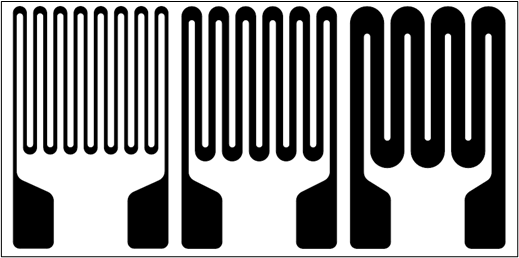
Designed gauge geometries with 1mm, 2mm, and 4mm printed thicknesses and end loops twice as thick as the printed width
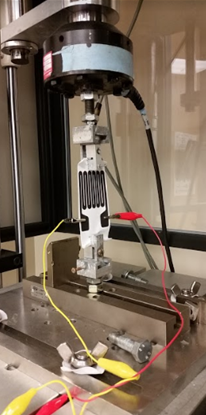
Testing strain resistance
Takeaways
Employing a rapid screening method can help to spur on the iteration process.
Due to complicated logistics, I often had to strategize with my teammates on how to come to the best solution for a problem with the information we had quickly. Often, we got stuck in our full testing loop, so we could have benefited from a tool to help us crank out more iterations, and thus more learnings.
Stakeholders come in all shapes and sizes.
They are not only within the obvious party – those directly involved and impacted – but also among the support systems, like our expert technicians without whom we would never have been able to achieve our project objectives.

Process
Research
Our first step was to do market research on the wearable technology industry. Understanding the different applications and how sensor mechanisms benefited users in those spaces was fundamental to contextualizing our performance objectives.
We also conducted technical research: I focused on printing and polymer materials while my teammates studied electro-mechanical effects in analogous technology to increase understanding of DuPont’s production techniques and the factors that would affect our design process, respectively.
In addition to our secondary research, we also met with representatives of two academic research labs at NC State University with concentrations in wearable technology to become more aware of the field and any issues the groups were facing as well as characterization capabilities on campus.
Testing & Ideation
With the aid of specialist technicians at the Analytical Instrumentation Facility (AIF) and a polymeric film tensile tester within NC State's Department of Biomedical Engineering, we managed cycles of physical and electro-mechanical characterization of samples first, with various combinations of inking and material parameters, and second, with our own gauge geometries, using a full factorial design of experiments.
These samples were produced at DuPont based on specifications we designated to assess our hypotheses and design requirements.
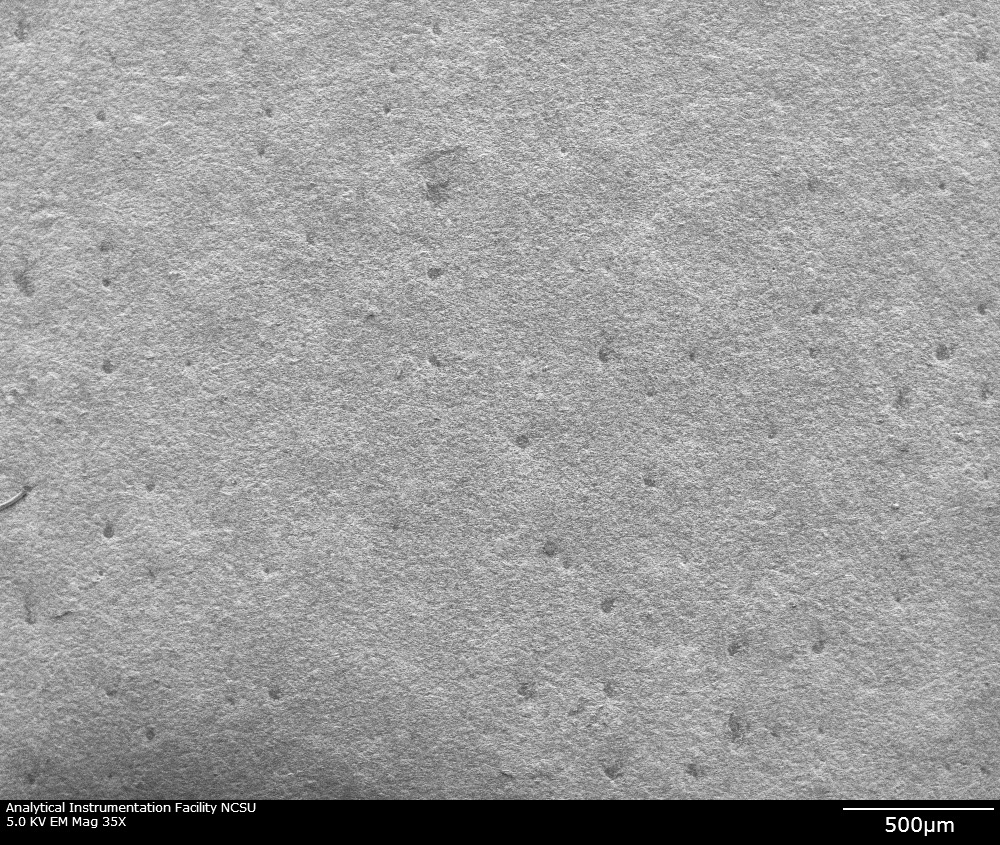
SEM, topographical view, 35x
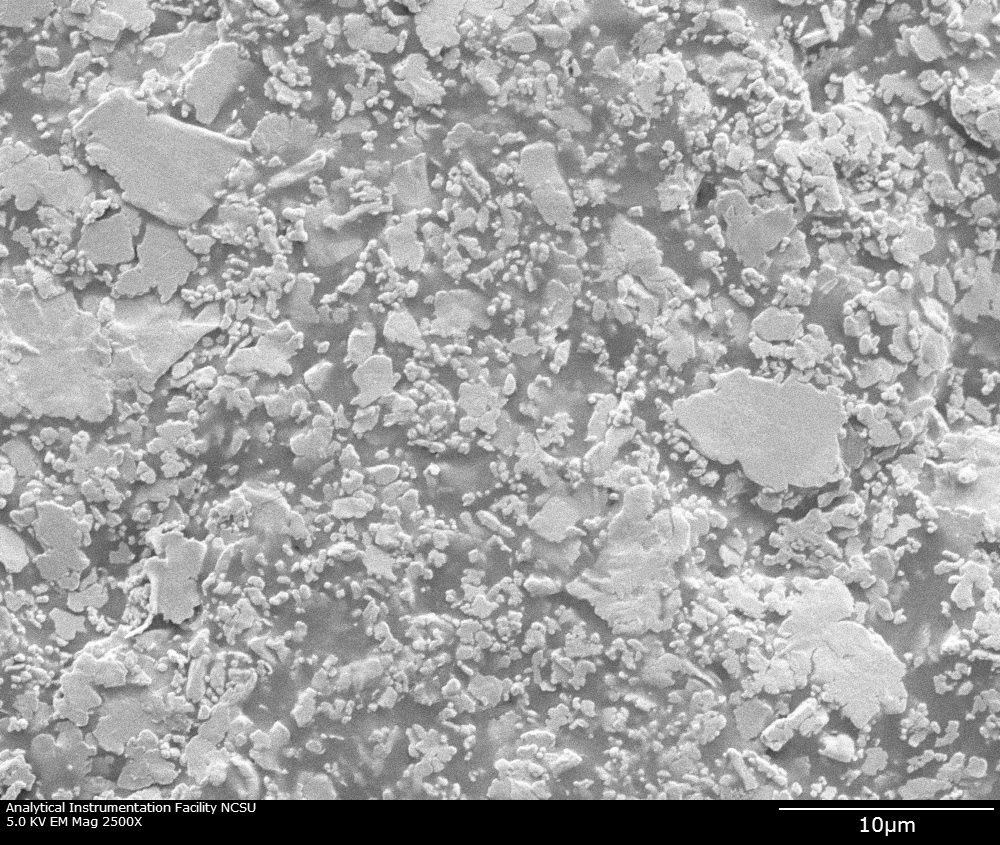
SEM, plane view, 2500x
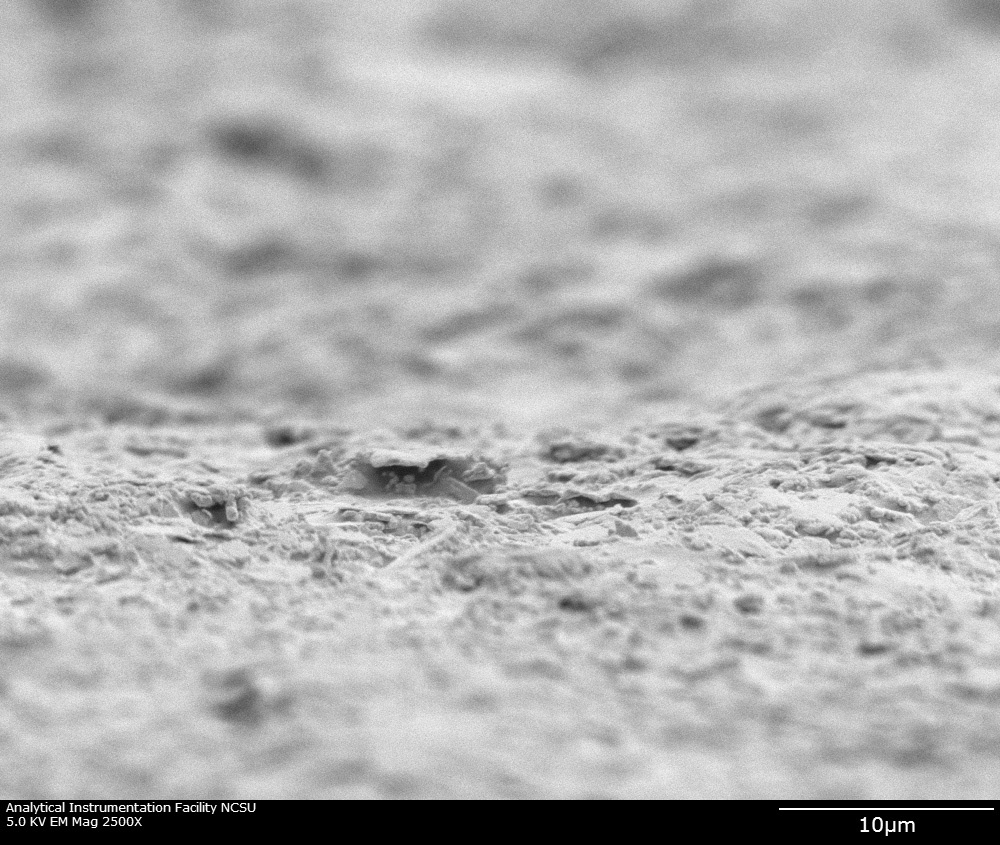
SEM, oblique view, 2500x
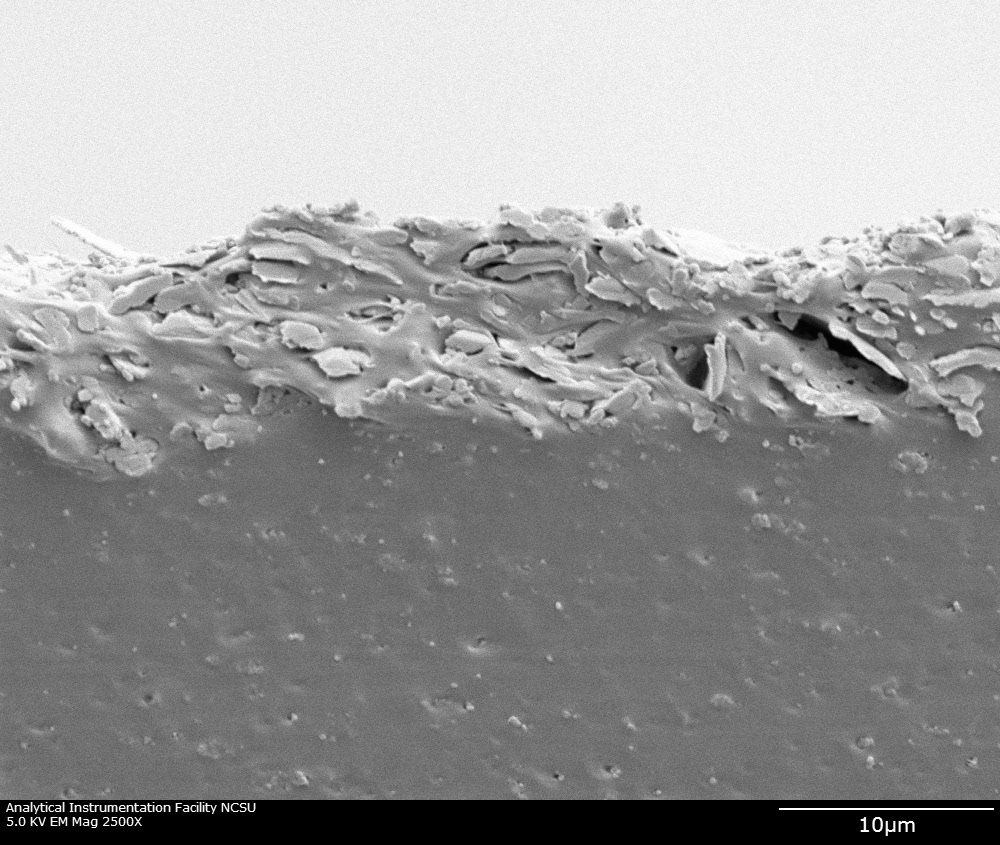
SEM Profile image of silver conductive polymer paste on Bemis tape
These images showing (from left to right) periodicity of the sample surface, the silver platelet network at certain strain conditions, and a cross-section of the sample, were taken using a Scanning Electron Microscope (SEM).